- A +
- A
- A -
The aircraft tail is part of the car's aerodynamic package. The main function of the rear wing is to reduce the lift at the rear of the vehicle. If the lift at the rear is greater than the lift at the front, it will easily lead to oversteer, reduced rear wheel grip, and poor high-speed stability.
1. For the hole positions on the aircraft tail, the traditional processing method is to use drawings to determine the drilling holes directly, which will cause the rivet hole positions to shift, leading to serious problems such as product scrapping.
2. Traditional measurement equipment is insufficient and inefficient to obtain data on the aircraft tail, and cannot obtain the curvature and size of the aircraft tail.
The aircraft tail is one of the important parts of the aircraft. The quality control of the aircraft tail is very important. Advanced design concepts and ideas are crucial to the subsequent aircraft tail. Through optimized design, the advantages of the aircraft tail can be better utilized and the aircraft tail can be fully utilized. Better structural and economic benefits. HOLON3D technical engineers quickly obtained high-precision 3D data of the aircraft tail through the industrial 3D scanner HL-3DS, imported the 3D data of the aircraft tail into the 3D reverse engineering software for secondary design, and successfully optimized the production plan of the aircraft tail.
Scanning device:
3D scanner HL-3DS
Features:
1. 13-step coding calibration technology: eliminate lens errors
2. Extrapolation method multi-frequency phase shift: uniform fringe projection
3. Compatible with photogrammetry system: higher accuracy
4. Granite calibration source
5. Patented design: Eliminates the problem of multi-angle scanning and splicing problems
6. The cumulative scanning accuracy is extremely high, and a single machine can scan a workpiece of about 4m.
7. Multi-mode scanning, easy to adjust
Actual picture of aircraft tail
3D scanning of aircraft tail
Aircraft tail scanning point cloud image
Aircraft tail scanning STL diagram
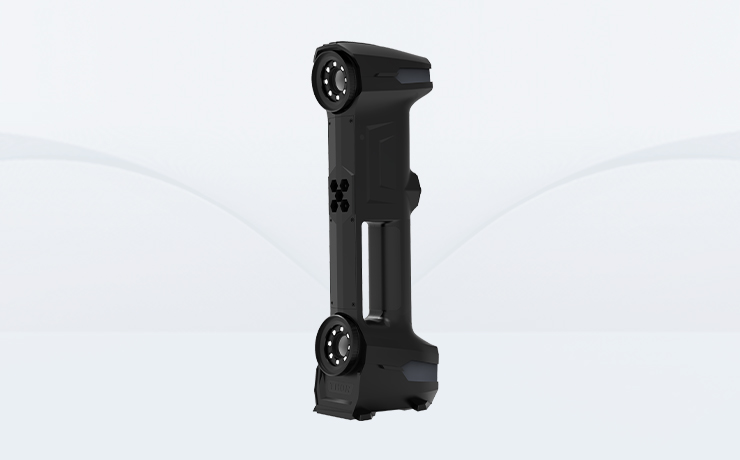
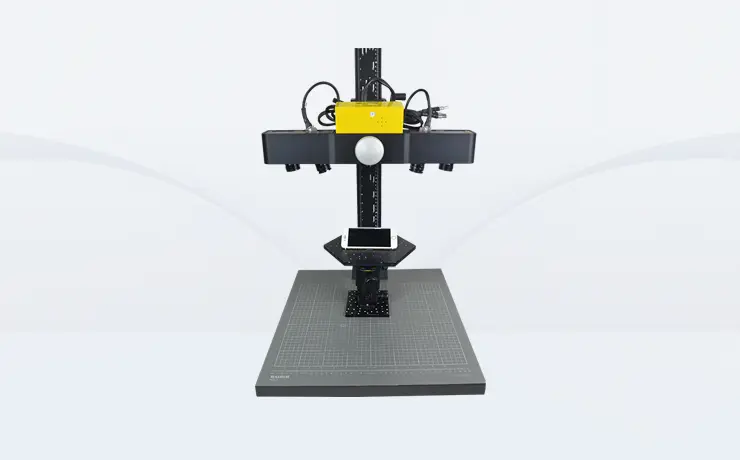
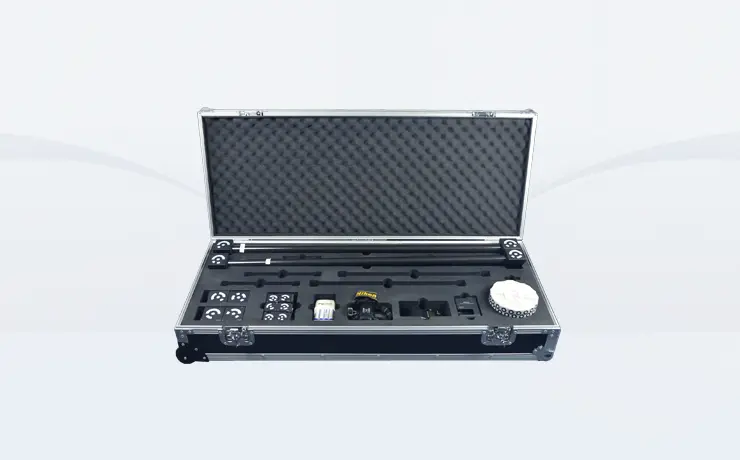