- A +
- A
- A -
Reverse engineering has been closely related to the industrial field, and the mold industry is no exception. The usage rate of molds in industrial production now reaches 60%-90%. Molds are divided into injection molding, blow molding, casting, forging, smelting, stamping, stretching, etc. They are tools used to shape items. This tool is composed of various parts, and different molds are composed of different parts. While reverse engineering is used for industrial inspection of workpieces, the modification and re-innovation of product design has become more and more routine and professional.
HOLON3D combines practice with in-depth understanding of the industry and customer needs to provide customers with comprehensive solutions and reverse product design to ensure that products comply with the applications and requirements of the mold industry and improve corporate competitiveness. High-quality extraction of point cloud data, high-efficiency assisted mold reverse engineering design (casting mold raw data acquisition, a process from the data collection end to the data processing end)
In the development and innovation of new products, many product data are not CAD digital models. Mold designers often have to deal with physical samples, and sometimes drawings may be missing. In this case, it is necessary to convert the physical objects through 3D scanning. Carry out three-dimensional reconstruction of the physical object for the CAD model, so as to design and manufacture the mold. Such as parting surface, calculation of shrinkage coefficient, etc.
Through the HOLON3D three-dimensional scanning system, the data shape and data size can be accurately grasped, using the latest scanning technology, such as white light three-dimensional scanning. For fine small parts or objects with complex appearance, the point cloud data of the object surface can be accurately extracted, and the single-frame scanning speed is less than 3 seconds, saving a lot of time in the work and thereby improving efficiency.
Mold manufacturing process
If the accuracy requirements are not met during the mold trial and trimming process, it may need to be redesigned. The use of reverse engineering technology can reduce the designer's troubles. Through the collection and re-innovation of object surface data, the redesign steps can be reduced, thereby optimizing the product design process.
Mold modification and repair
Traditional mold design generally uses three-dimensional engraving and CNC milling machines to make proportional molds for products. This method cannot create digital files, requires a large amount of manual repair work, requires high skills of workers, and brings great difficulties to later CNC processing and industrial inspection. Since the finished product often inherits the advantages and disadvantages of the master mold, this technology is gradually integrated into reverse engineering to improve the modification and reinnovation capabilities of the mold.
After the design and production of the mold is completed, the prototyped mold product may be unsatisfactory. In this case, the mold needs to be modified and innovated. Re-inspection and modification of molds are often complex processes. In the mouths of some designers, there is a saying: "It is better to redesign than to modify." At this time, three-dimensional detection methods can be used for detection and reverse design, reducing the extra work of designers.
Make accurate error quality reports such as deformation of mold samples, master detailed three-dimensional inspection results, and improve product quality. Many companies use 3D scanning technology and use 3D scanning equipment to conduct shape evaluation during the molding stage. Generate CAD data comparison analysis and color error coding diagrams. If defects are detected during dimensional inspection of production prototypes, the defects can be fed back into the die design and processing methods at an early stage, thereby improving development efficiency.
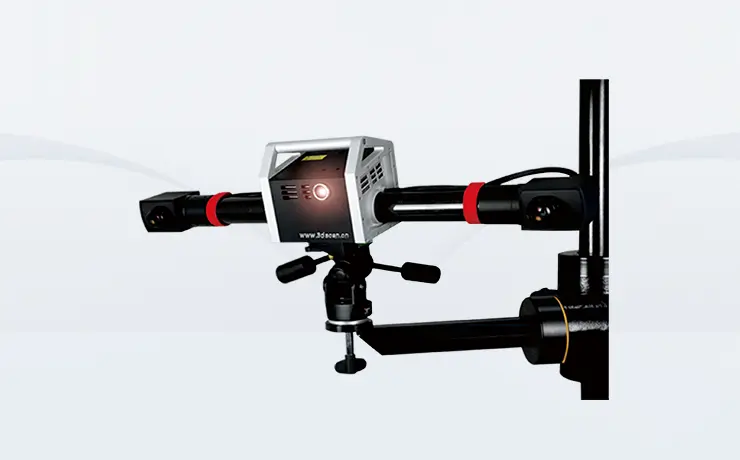
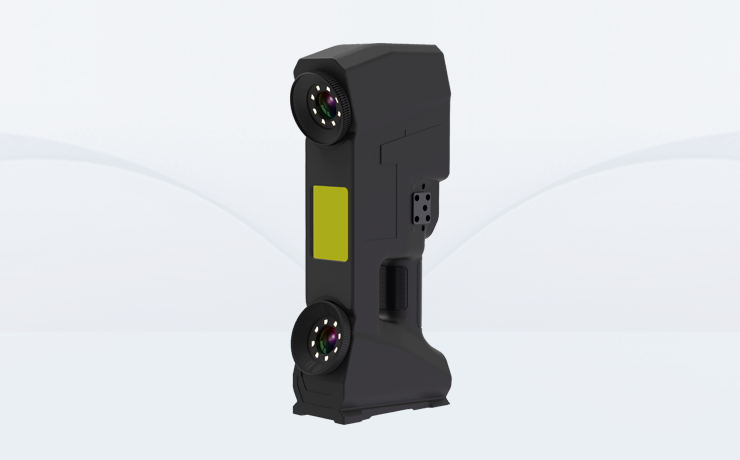
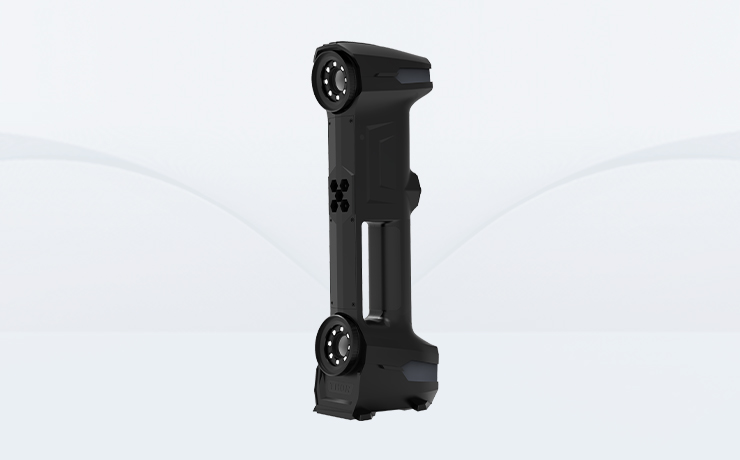