- A +
- A
- A -
Blades are key parts of aero-engines, and their manufacturing volume accounts for about one-third of the entire aircraft manufacturing volume. Aeroengine blades are thin-walled and easily deformed parts. How to control its deformation and process it efficiently and with high quality is one of the important topics in the current blade manufacturing industry.
1. Use a handheld 3D scanner to detect the engine blades, compare the obtained 3D data with standard parts, the accuracy requirement is 0.02mm, and process the unqualified parts.
2. Using traditional measurement methods (inspection tools, fixtures, three-dimensional coordinates, etc.), the data obtained is incomplete, and curved surfaces cannot be measured, resulting in incomplete data acquisition and subsequent work planning.
Actual picture of engine blade
Equipment used: Handheld 3D scanner Model 37
Using all-blue laser scanning, the scanning speed is 2,070,000 measurements/second, dual industrial cameras, automatic stitching technology of landmark points and independently developed scanning software have high scanning accuracy and work efficiency. By comparing with the original data, errors in actual processing are detected.
Engine blade STL data chart
Engine blade comparison inspection chart
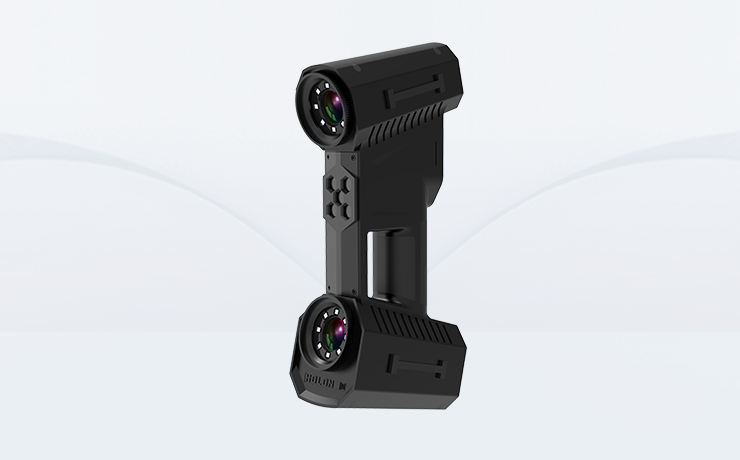

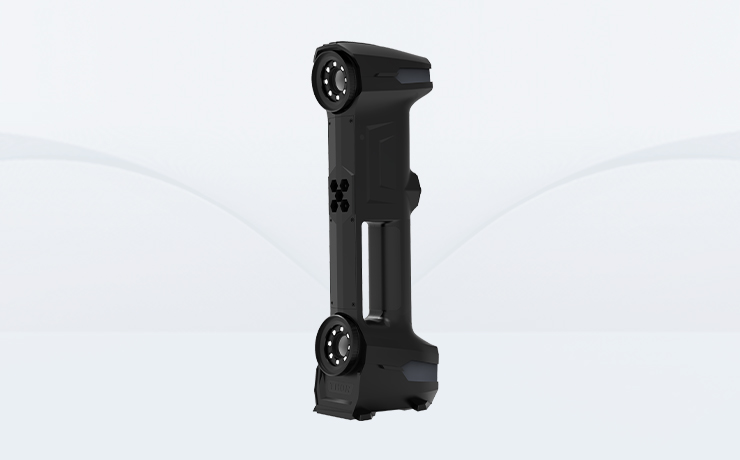