- A +
- A
- A -
Wind is a new energy source with great potential. At present, the energy obtained from burning coal every year in the world is only one-third of the energy provided by wind power in a year. Therefore, domestic and foreign governments attach great importance to the use of wind power to generate electricity and develop new energy sources. Blades are the most basic and critical components of wind turbines. Their good design, reliable quality and superior performance are the decisive factors in ensuring the normal and stable operation of the unit.
1. When performing three-dimensional measurement of blades, due to the large size of the measured object, the cumulative error will be too large when measured with a camera-type three-dimensional scanner. How to eliminate the impact of the error is the biggest problem.
2. There are many curved surfaces in the blade shape, and it is difficult for light to shine in some places, making scanning more difficult.
3. The traditional measurement method has limited data and cannot accurately express the three-dimensional data of the wind turbine blade surface, nor can it be used for later secondary design and quality.
Blades are the most basic and critical components of wind turbines. Their good design, reliable quality and superior performance are the decisive factors in ensuring the normal and stable operation of the unit. The customer uses a 3D scanner + 3D photogrammetry system HL-3DP to obtain 3D data of wind turbine blades, improve the blade structure, and enhance blade performance.
wind turbine blades
In view of the large area of wind turbine blades and many curved surfaces, Hualang 3D engineers proposed a solution using: 3D photogrammetry system HL-3DP (calculates the 3D coordinate values of key information points on the surface of wind turbine blades) + 3D scanner HL-3DWV+ (quickly obtain high-precision three-dimensional data of wind turbine blades) + reverse design software (convert wind turbine blade point cloud data into triangular mesh surface data) + post-processing in the design software to design wind turbine blades secondary design.
a. Hualang 3D engineers use the 3D photogrammetry system HL-3DP to photograph the tested blades from different angles, and then import the captured pictures into the photogrammetry software. The software will automatically calculate the overall shape of the tested blades based on the triangulation principle. Frame points. Then the software calculates the frame points of the wind turbine blades and imports them into the three-dimensional scanning software HLOLON3DS. The frame point data will be used as the positioning skeleton to splice the scanned data, thereby effectively eliminating cumulative errors and achieving the best three-dimensional measurement accuracy.
b. The three-dimensional scanner HL-3DWV+ conducts comprehensive three-dimensional measurements of long wind turbine blades and obtains three-dimensional measurement data of wind turbine blades.
c. Use reverse design software to analyze the deviation of the digital model size of the high-quality surface model, and then make design adjustments based on the analysis results.
d. Using the CAD data finally output by the reverse modeling software, it can be used for CNC machine tool processing, rapid prototyping, appearance quality inspection and other applications.
3D data of wind turbine blades
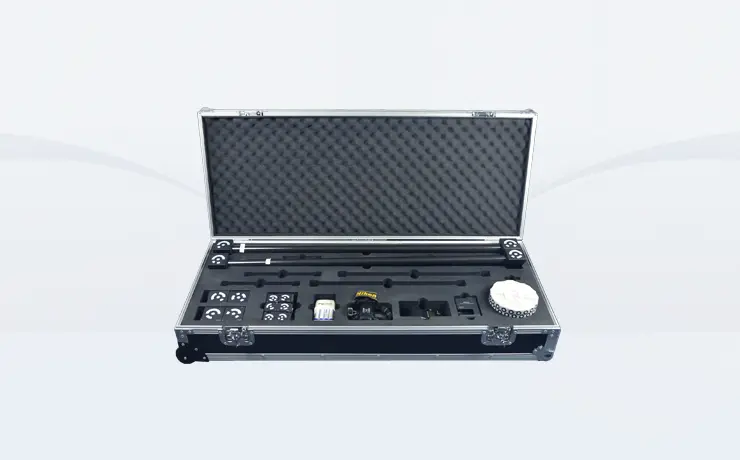
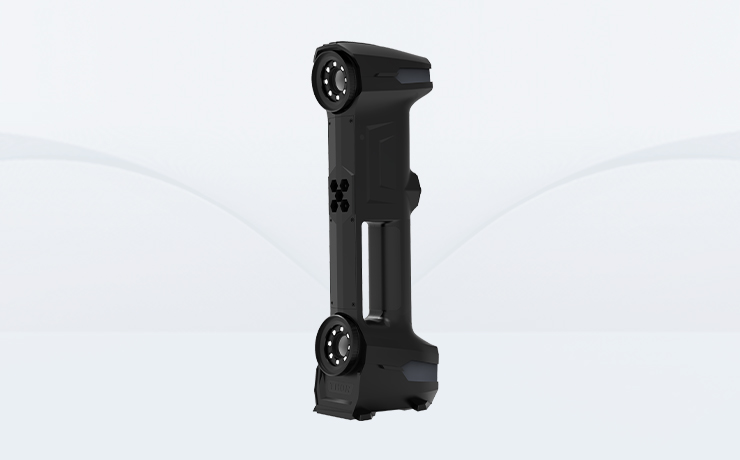
