- A +
- A
- A -
In the production process of ultra-large forged parts, the technical parameters and performance indicators have very high standards. The forging process is very complex, requires high precision, and is difficult to forge. A domestic heavy equipment manufacturing company hopes to use the HOLON3D scanner to inspect and analyze the ultra-large forgings produced, and obtain inspection data reports to meet product improvement needs.
1. Due to the large volume of ultra-large forgings, traditional measuring equipment cannot measure and produce written inspection reports, making measurement very difficult.
2. Ultra-large forgings are large in size, with a diameter of 10 meters. To scan these large forgings, a large-format 3D scanner must be used. Using other 3D scanners will take longer to scan, have low accuracy, and require a large amount of scanning data. The data ultimately cannot be fully spliced.
This heavy equipment manufacturer has very high requirements for the production of ultra-large forged parts. In order to solve the problem of difficult inspection of ultra-large forged parts, the heavy equipment enterprise contacted HOLON3D, hoping to solve the problem of difficult inspection and requested 3D scanning. The scanning speed and accuracy of the instrument must be guaranteed to complete the scanning work under the premise of ensuring its customer needs.
1. Preparatory work
Spray developer: Improve the contrast of the background color on the surface of the sample to obtain better scanning data.
Attach landmark points: The acquired data can be positioned and spliced in the scanning software.
Paste coding points: enable the three-dimensional photogrammetry system to obtain the 3D coordinate values of the object surface.
2. Three-dimensional photogrammetry
HOLON3D engineers use a three-dimensional photogrammetry system to obtain the 3D coordinates of the surface of ultra-large forgings, and use a three-dimensional photogrammetry system (HL-3DS+) to take multiple images of nuclear forgings. Through three-dimensional ranging, the HOLON3D software automatically combines these images. After calculation, the 3D coordinates of the center of each coding point can be obtained, and the 3D coordinates of the key information points on the surface of the object can be calculated.
Super large forgings about 10 meters in diameter and 2 meters high
Scanning site for super large forgings with a diameter of about 10 meters and a height of 2 meters
3. 3D scanning
Import the 3D coordinate data of the surface of the ultra-large forgings into the HOLON3D scanning system, and use the 3D scanner α7000 to quickly scan and obtain the 3D data of the ultra-large forgings. This 3D scanner has the characteristics of large scanning format, fast scanning speed, and high equipment stability. Using the 3D photogrammetry system (HL-3DP) in conjunction with the 3D scanner α7000 can correct the point cloud information of large-area curved surfaces, greatly improving the overall point cloud splicing accuracy of the 3D scanner and improving work efficiency. It only takes 2 hours to obtain the three-dimensional data of nuclear forgings, compare and analyze the original digital model of the ultra-large forgings with the three-dimensional scanning data, and obtain a detection report.
3D scanning point cloud image of ultra-large forging parts
3D scanning STL diagram of ultra-large forging parts
Three-dimensional inspection chart of super large forgings
Cross-sectional analysis diagram of super large forging parts
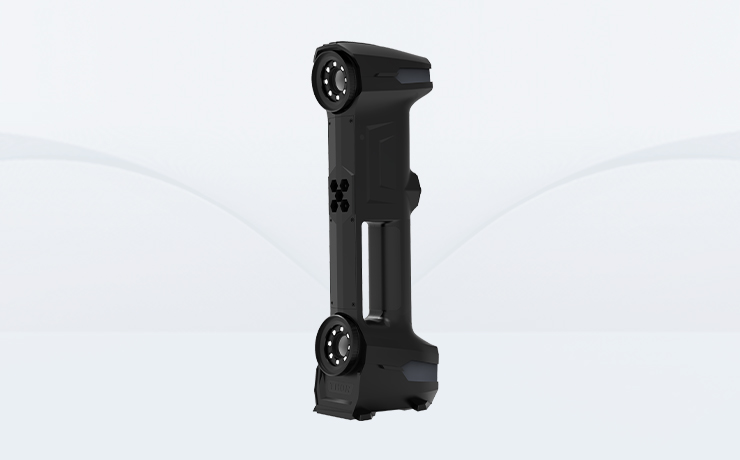
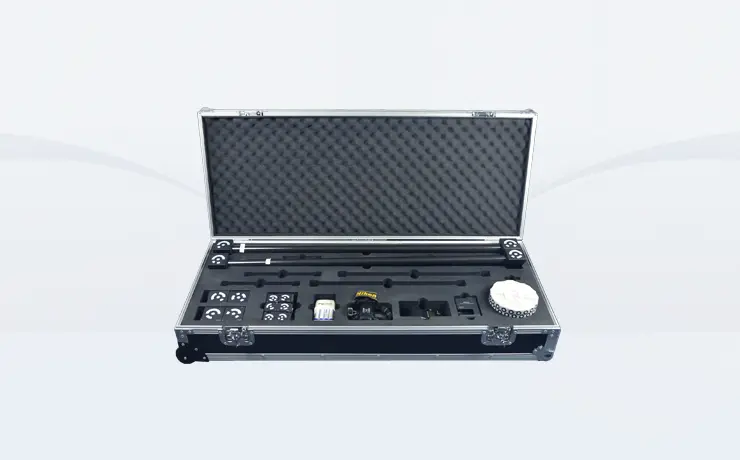
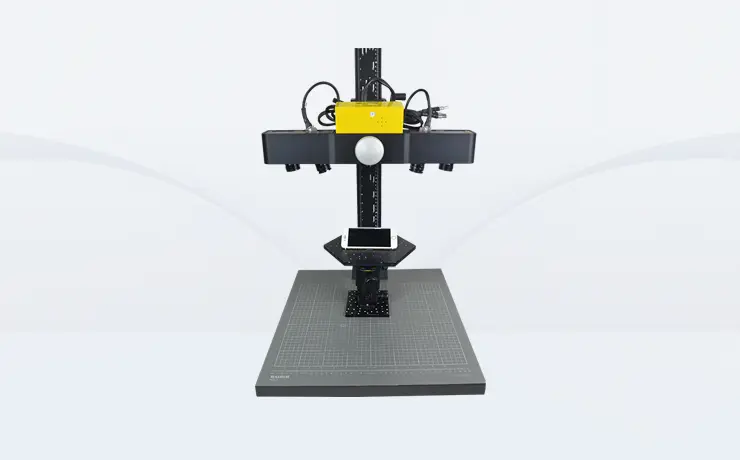